If you’re new to manufacturing, the terms Takt Time, Cycle Time, and Lead Time can be confusing. But don’t worry, we’re here to help! Quidlo comes with a beginner guide to Takt Time, Cycle Time, and Lead Time where we’ll explain each term and give you some examples so you can see how they work in practice. Plus, we’ve got calculators to help you figure out your own numbers. Let’s get to the basics first!
Table of Contents
Takt Time vs Lead Time vs Cycle Time: What’s The difference
When it comes to manufacturing and production processes, there are a lot of confusing terms being thrown around. One particularly tricky trio? Lead time, cycle time, and takt time. While they may sound similar, these measurements actually have fairly distinct meanings. Before diving into detail, let’s get an insight into the basics.
Takt Time measures how quickly work needs to be completed in order to meet customer demand. It is calculated by dividing the available time by customer demand.
Cycle Time measures the time it takes for a specific process or task to be completed. It does not include any periods of waiting or delays, just the actual amount of time spent actively working on something.
Lead Time measures the time it takes for a product to be completed from start to finish. This includes planning and processing, as well as any periods of waiting or delays.
So while all three terms involve measuring time, they each have their own unique focuses and calculations. Now, let’s get into the detailed version of the tricky trio.
What is Takt Time?
Have you ever heard of the “beat” in a production line? This beat is known as Takt Time, a term derived from the German word Takt, meaning rhythm or cycle. In Lean Manufacturing, Takt Time is used to set the pace for production, ensuring that products are being produced at a steady rate to meet customer demand. In essence, takt time is the rate at which products must be produced in order to meet customer demand. It allows organizations to identify bottlenecks in their production process and make adjustments to ensure they are working at peak efficiency. By calculating Takt Time and implementing it on the production line, businesses can achieve a smooth flow and minimize wasted time and resources.
How is Takt Time Calculated?
You must have heard the adage, “time is money”. In the realm of Lean production, that idiom has a very literal meaning. To increase efficiency and productivity, companies use a formula called Takt Time to calculate the available production time for each product. Simply put, Takt Time is determined by taking the total available working time and dividing it by the customer demand for a specific product.
Here’s a formula for it:
Takt time = Production Time / Consumer Demand
For example, if a company has eight hours of production time per day and their customer demands 100 units per day, the takt time would be calculated as 8 hours divided by 100 units, or 480 minutes (or 8 minutes) per unit.
Keeping track of Takt Time helps manufacturers plan their production and determine if they need to adjust their workflow or processes to meet customer demands on time. It’s all about finding that sweet spot between meeting customer needs and maximizing resources – because in business, time really is money.
Real World Examples Of Takt Time
Takt time isn’t just a fancy term used in manufacturing; it has practical applications in many industries.
Some major names in the industry have incorporated Takt time into their operations.
Automotive giants Toyota and Honda have used it to streamline their assembly lines.
In the food industry, McDonald’s and Nestle have both used Takt time to increase productivity. Even the high-end luxury brand Louis Vuitton employs this method in its production processes.
By utilizing Takt time, these companies have been able to keep up with consumer demand and achieve a higher level of efficiency in their production processes. The following are other real-world examples of Takt Time.
The e-commerce giant tracks customer behavior and buying patterns to determine how many items need to be produced and shipped at any given moment. This allows them to keep inventory low while still meeting consumer demand.
- Automotive assembly lines
Factories use takt time to ensure their production matches market demand for certain car models. This not only maximizes efficiency but also ensures that the factory isn’t left with a surplus of unpopular cars.
- Hospitals
Takt time is used in hospitals to track patient flow in emergency rooms and schedule doctors’ shifts accordingly. This helps increase efficiency and improve patient satisfaction by ensuring they receive timely care without excessive wait times.
As these real world examples show, takt time can be utilized across a variety of industries to streamline production, increase productivity and meet consumer demand effectively.
Takt Time Calculator
Are you tired of manually calculating Takt time on Excel? Look no further, because Quidlo has the solution for you! Our Excel Takt Time Calculator will revolutionize the way you approach production scheduling. Simply input your target output and operating time, and our calculator will instantly calculate your required takt time. Say goodbye to manual calculations and stressful scheduling decisions – let Quidlo handle it for you! Try out our sample calculator now, and experience the ease and efficiency of automating takt time calculations.
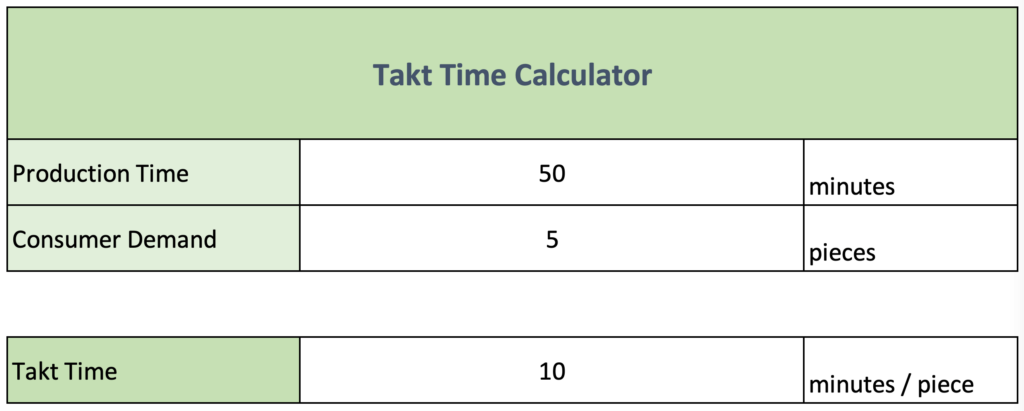
What is Cycle Time?
Cycle time is simply the amount of time it takes for a task or process to be completed, from start to finish. By identifying these cycles and finding ways to reduce or streamline them, businesses can increase efficiency and meet deadlines more effectively.
The cycle time formula can reveal a lot about the efficiency of your business operation. By tracking how long it takes to complete a product or deliver a service, you can identify and address any bottlenecks in your process. This in turn can lead to improved performance and delivery speed and higher customer satisfaction. And while cycle time may seem like just one small metric, its effects can ripple throughout every aspect of your business.
How is Cycle Time Calculated?
Cycle time is calculated by dividing the net production time (or how long it takes to actually create a product) by the number of units produced. Sounds simple enough, right? The lower the cycle time, the faster a company is able to produce their goods and meet consumer demand.
The equation goes like:
Cycle Time = Net Production Time (NPT) / Units Produced
When it comes to calculating cycle time, the numbers don’t lie. Remember: the net production time is a precise measurement of how long it takes to actually complete the task or produce the product. Take breaks and waiting times out of the equation – they only serve as distractions from the true measure of efficiency.
Real World Examples Of Cycle Time
Cycle time is the amount of time it takes to complete a task, from start to finish. And you probably encounter it more often than you think! One common example is at wash-and-fold laundry services: the cycle time would be the total time it takes for an employee to gather, wash, dry, and fold your clothing. In manufacturing, cycle time might refer to the amount of time it takes for a machine to complete one unit of a product.
Major companies have already discovered the power of this simple yet effective tool: Amazon, Procter & Gamble, Boeing, and Honda. By measuring and analyzing the amount of time it takes to complete a task or process, these companies are able to make necessary adjustments in order to streamline their operations and improve productivity. The following are some other real-world examples of Cycle Time.
- In the medical field, hospitals use cycle time to track the length of each patient’s visit and ensure efficient use of resources.
- In the fashion industry, clothing manufacturers analyze their cycle times to determine how quickly they can produce garments and meet demands from retailers.
- Cycle time is also important for transportation companies like airlines as they plan flight schedules and calculate turnaround times for aircrafts.
- In the fast food industry, restaurants use cycle time to monitor wait times and increase customer satisfaction.
- Warehouses track cycle time to optimize their shipping processes and meet deadlines for delivery orders.
- The automotive industry uses cycle time in their assembly lines to improve efficiency and ensure quality control in their production processes.
- In the construction industry, contractors measure cycle time to schedule tasks and keep projects on time and within budget.
As you can see, businesses across various industries rely on cycle time to stay competitive, improve their team dynamics and provide excellent service to their clients.
Cycle Time Calculator
Are you tired of the endless cycle of waiting for results? Say goodbye to the days of counting down the seconds until that big project is done with our Cycle Time Calculator. Simply input your data, and we’ll crunch the numbers for you. No more stress or frustration- just efficient and accurate results every time. Start optimizing your process and streamlining your workflow today with Quidlo’s Cycle Time Calculator.
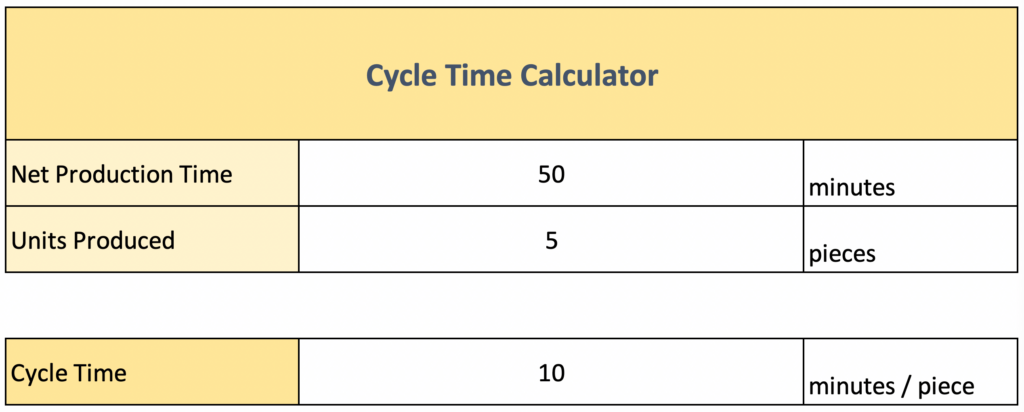
Takt Time vs Cycle Time
Are you a little confused about the distinction between Takt Time and Cycle Time? You’re not alone. Here are five key differences to keep in mind:
- Takt Time is based on customer demand, while Cycle Time is based on the actual time it takes to complete a task.
- Takt Time is a target or goal, while Cycle Time measures the actual time spent on a task.
- Takt Time can be adjusted throughout production, while Cycle Time remains constant.
- Takt Time is used in lean manufacturing, while Cycle Time can be used in any type of production process.
- Improving Takt Time involves adjusting the production process, while improving Cycle Time involves improving individual performance or efficiency.
So remember: Takt sets the pace, but Cycle tells you how quickly you’re actually moving!
What is Lead Time?
Lead time simply refers to the amount of time it takes for a process to be completed, from start to finish. In manufacturing, for example, lead time would refer to the amount of time it takes to purchase raw materials, produce the product, and deliver it to customers.
Long lead time can mean missed opportunities, delayed products, and lost profits. On the flip side, a shorter lead time means quicker decision-making and faster turnarounds for sales and manufacturing processes.
The key to achieving a shorter lead time is finding ways to streamline and simplify processes in order to cut out unnecessary steps or delays. This can involve implementing new technologies or rethinking traditional methods of operation. Etching out a quicker lead time may require some initial effort, but the end result will pay off in increased efficiency and a stronger bottom line.
How is Lead Time Calculated?
The world of business and manufacturing is all about productivity and efficiency, and lead time plays a major role in this equation. But how do we calculate lead time? Break it down into its components: pre-processing, processing, and post-processing. You add up all these chunks of time, and voila – you have your lead time. Of course, each component may be defined differently depending on the specific industry or process, but the general formula remains the same.
The formula for lead time is:
Lead Time = Pre-Processing Time + Processing Time + Post-Processing Time
When it comes to lead time, it’s all about the three Ps: pre-processing, processing, and post-processing. Pre-processing refers to any steps that need to happen before the actual processing can begin – for example, gathering materials or setting up equipment. Processing is the main event – this is where the work actually takes place. And finally, post-processing includes wrapping up loose ends, such as packaging completed products or sending out invoices.
Lead Time Examples
When it comes to lead times, understanding the concept is just the beginning. It’s also important to know how they can affect your niche-specific business. So let’s take a look at some of the most common lead times and how they can impact your business processes.
Lead Time in Supply Chain Management
In the world of supply chain management, there’s nothing quite as frustrating as not knowing when your materials will arrive. Unfortunately, this issue is all too common due to the varying lead times among suppliers. That’s where lead time scheduling comes in: Lead time refers to the amount of time it takes for a product to go from being ordered or produced to arriving at its final destination.
This process involves multiple steps, including ordering materials, manufacturing the product, packaging and shipping, and finally delivery. Each step adds additional lead time, and delays can easily pop up along the way. By coordinating with suppliers and ensuring necessary components arrive together, production flow is streamlined and there are reduced expenses related to shipping and receiving.
Lead Time in Manufacturing
When it comes to manufacturing products, timing is everything. In the business world, we refer to this timing as lead time – the amount of time it takes for a product to go from the initial design stage all the way through production and delivery.
Lead time can have a major impact on a company’s bottom line – shorter lead times mean quicker delivery and increased customer satisfaction, while longer lead times can lead to missed sales opportunities and lost profits. Having efficient systems in place to minimize lead time can give manufacturers a competitive edge in today’s fast-paced market.
Lead Time in Project Management
When it comes to project management, there’s one crucial factor that can throw even the best-laid plans into disarray: lead time. This refers to the amount of time it takes for a task or product to go from planning stages to completion. Lead time can vary greatly depending on a number of factors, including available resources and unforeseen roadblocks.
It’s important for project managers to account for potential lead time issues in their planning process, ensuring that they have enough leeway in their timeline to accommodate any potential delays without impacting their overall project goals. The key is always staying ahead of the game and leaving plenty of room for the unexpected – because when it comes to lead time, Murphy’s Law reigns supreme.
Lead Time Calculator
Are you tired of outdated and inefficient methods for calculating lead time? Well, say goodbye to those days and say hello to the Quidlo’s Lead Time Calculator! This Excel spreadsheet makes calculating lead time a breeze, with simple input fields for pre-processing, processing, and post-processing time. Just plug in your data and let the calculations do the work. Never struggle with lead time again with the Quidlo’s Lead Time Calculator.
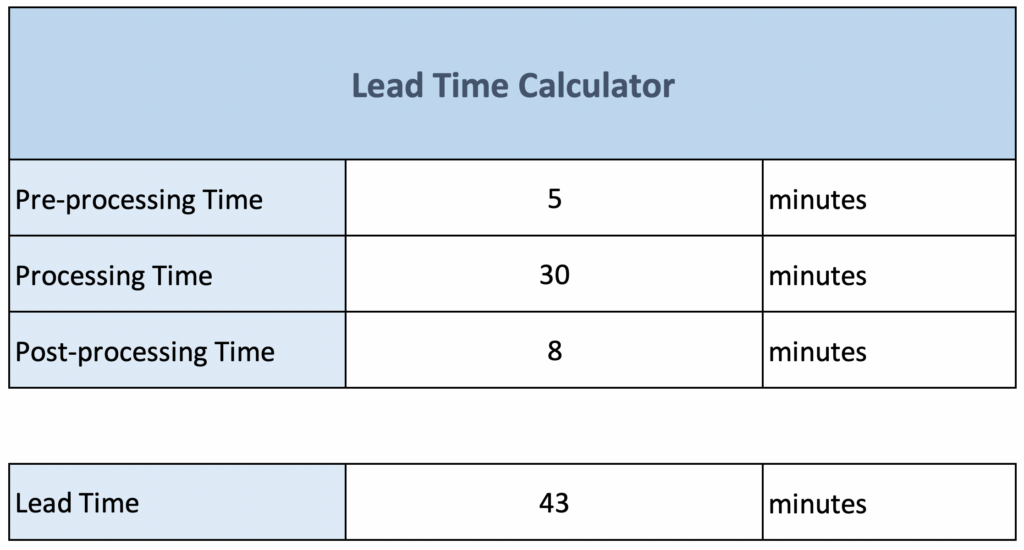
Lead Time vs Cycle Time
Looking to improve your project management skills? It’s important to understand the difference between Lead Time and Cycle Time. Here’s a quick rundown of the top five ways these metrics differ:
- Lead Time is the total time that passes from the start to finish of a task, while Cycle Time only measures the active work involved in completing the task.
- Lead Time includes any delays or idle periods, while Cycle Time focuses solely on productive work.
- Lead Time measures the timeframe for a single task, while Cycle Time can be measured for multiple tasks in a workflow.
- Lead Time is often used to plan deadlines and schedules, while Cycle Time is used for process optimization and improvement.
- Lead Time can be affected by external factors, while Cycle Time is more closely tied to internal processes and team performance.
Understanding these key differences can help you track progress and improve efficiency in your projects.
Tracking Lead, Cycle, and Takt Time
Are you tired of feeling like your work processes are disorganized and inefficient? Are you constantly struggling to keep track of how much time it takes to complete tasks, or how long it takes for projects to go from start to finish? Well, let Quidlo Timesheets and Takt Time, Cycle Time, and Lead Time calculators help take the stress out of keeping track of time and calculations. These calculators can make it easy for your team to stay organized and ensure that workflows are running smoothly.
Final Thoughts
As a business, it’s important to be aware of the different types of time measurements and what they mean for your production process. Understanding Lead Time, Cycle Time, and Takt Time can help you optimize your processes and improve your bottom line. The Quidlo Time Tracking Software is an easy way to track time needed for calculating all three of these so that you can start seeing improvements in your manufacturing or service-based business. Have you tried using Quidlo yet? If not, give it a try and see how it can help streamline your operations.